Os últimos dois anos (2015 e 2016) puderam ser considerados como o ponto de partida para impressão direta de metal (DMP) no setor aeroespacial, já que a tecnologia deu um salto da prototipagem para peças de produção e montagens prontas para voo.
Durante esse período, a Airbus Defence and Space trabalhou com a 3D Systems para fazer um grande avanço: o primeiro filtro de radiofrequência (RF) impresso em 3D testado e validado para uso em satélites comerciais de telecomunicações. O projeto foi construído com base em pesquisa financiada pela Agência Espacial Europeia (A0/1-6776/11/NL/GLC: Modelagem e design de componentes de guia de ondas utilizando técnicas de fabricação 3D).
Os filtros metálicos de RF ou de guia de ondas datam dos primeiros sistemas de comunicação espacial há quase 50 anos. Os filtros agem como policiais de trânsito, permitindo a passagem de frequências de canais selecionados e rejeitando as de sinais fora desses canais.
Uma grande tendência do setor é aumentar a capacidade de vários feixes em um único satélite. Um satélite de alta capacidade como o Eutelstat KA-SAT fabricado pela Airbus Defence and Space transporta quase 500 filtros de RF e mais de 600 guias de ondas. Muitas delas são projetadas sob medida para lidar com frequências específicas.
Cumprindo exigências essenciais
Os satélites de telecomunicações exemplificam a ênfase incansável do setor aeroespacial na redução do peso — enviar um veículo para uma órbita geoestacionária pode custar até US$ 20.000 por quilograma. A inovação contínua no design e a redução do tempo de produção também são as principais prioridades, já que a maioria dos satélites é projetada para uma vida útil de 10–15 anos.
Essas prioridades fazem dos satélites de telecomunicações os candidatos ideais para a impressão direta de metal. O 3D Systems ProX® DMP 320 utilizado no projeto do filtro de RF da Airbus permite aos fabricantes consolidar peças, melhorar a funcionalidade com formas e superfícies que não podem ser fabricadas por meios tradicionais, reduzir o tempo de produção e diminuir os custos para designs personalizados, além de diminuir o peso enquanto mantém ou melhora a resistência do material.
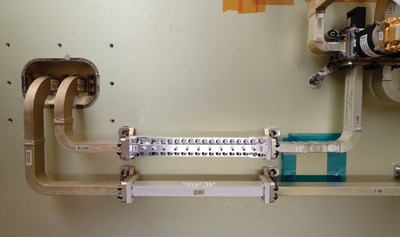
Nova aplicação para a impressora comprovada
A instalação da 3D Systems em Leuven, na Bélgica, vem usando a ProX DMP 320 da 3D Systems desde que a máquina estava em seus estágios beta. Os projetos bem-sucedidos incluem otimização topológica, redução de peso e consolidação de peças para peças validadas para voos espaciais, como suportes e acessórios finais de suporte para satélites de telecomunicações. O projeto da Airbus Defence and Space foi a primeira incursão da 3D Systems de Leuven em filtros de RF.
O ProX DMP 320 é projetado para oferecer alta precisão e alto rendimento em ambientes de produção exigentes 24/7. Sua ampla gama de ligas LaserForm (titânio, aços inoxidáveis, alumínio, cromo de níquel e cromo cobalto) é formulada e ajustada para que esta impressora de metal possa fornecer peças de alta qualidade e propriedades consistentes.
Os módulos de fabricação intercambiáveis oferecem maior versatilidade das aplicações e menos tempo de inatividade quando se movem entre diferentes materiais de peças. Uma câmara de construção a vácuo controlada garante que cada peça seja impressa com as propriedades do material, a densidade e a pureza química comprovadas.
Inovação em design disruptivo
O projeto de filtro de RF da Airbus Defence and Space demonstra a capacidade da impressão 3D de permitir a inovação em design de peças aeroespaciais que não mudaram sensivelmente em décadas.
Os filtros de RF são tradicionalmente projetados com base em bibliotecas de elementos padronizados, tais como cavidades retangulares e seções transversais de guia de onda com curvas perpendiculares. As formas e as conexões são ditadas pelos processos típicos de fabricação, como a moagem e o desgaste. Como resultado, as cavidades para filtros de RF normalmente precisam ser usinadas em duas metades juntas. Esse procedimento aumenta o peso, acrescenta uma etapa de montagem ao tempo de produção e exige uma
avaliação de qualidade extra.
Projetar as peças para impressão 3D permitiu que a Airbus Defence and Space explorasse geometrias complexas sem custo de fabricação adicional.
A CST MWS, uma ferramenta de software de simulação eletromagnética 3D padrão, foi usada para projetar os filtros de RF impressos em 3D, com pouco tempo gasto na otimização. O aumento da flexibilidade de fabricação viabilizado pela impressão 3D produziu um design usando uma supercavidade elipsoidal pressionada. A forma única ajudou a canalizar as correntes de RF e proporcionar as compensações necessárias entre o fator Q — uma medida de eficiência de um guia de ondas baseada na perda de energia — e a rejeição dos
sinais fora da banda.
"A inovação disruptiva reside no fato de que a funcionalidade pura, não a capacidade de fabricação, agora determina como o hardware será projetado", afirma Koen Huybrechts, engenheiro de projetos da 3D Systems em Leuven. "Este projeto é um exemplo clássico de 'a forma segue a função'".
"Os principais benefícios de um design monolítico possibilitado pela impressão 3D são a massa, o custo e o tempo", afirma Paul Booth, o engenheiro de RF da Airbus Defence and Space em Stevenage, no Reino Unido. "A massa é reduzida porque não há mais a necessidade de ter fixadores. Com a impressão direta de metal há também o bônus de ausência de custos para que o perfil externo siga mais de perto o perfil interno, portanto, somente o metal realmente necessário precisa ser usado. O benefício do custo/tempo vem da redução na montagem e no pós-processamento."
Eliminando as preocupações com a superfície
Inicialmente, a topologia diferente da superfície em peças de metal impressas em 3D era considerada um problema, mas testes extensivos realizados pela Airbus Defence and Space eliminaram essas preocupações.
"A topologia microscópica é diferente na parte impressa em 3D do que em uma peça usinada", declara Booth. "As superfícies usinadas têm picos e canais afiados, enquanto a superfície impressa em 3D é esferoidal derretida para que haja menos vincos."
"A forma esférica das partículas de pó utilizadas na impressão de metal 3D ocasiona uma certa ondulação em vez de transições íngremes", afirma Huybrechts, "mas a capacidade de moldar uma peça para uma filtragem de sinal mais eficaz supera qualquer preocupação com a topologia de superfície".
"Ficamos muito satisfeitos com o trabalho que a 3D Systems fez e muitos na Airbus comentaram o quanto é bom o acabamento da superfície", declara Booth. "Fizemos algumas tomografias de raio X e ficamos impressionados com a densidade da peça e com a qualidade geral da superfície".
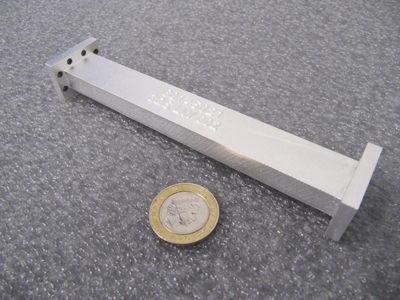
Aprovação em testes rigorosos
Três amostras de alumínio impressas na ProX DMP 320 usando caminhos de processamento diferentes foram testadas pela Airbus Defense and Space em suas instalações de Stevenage. Os testes imitam as condições que as peças enfrentariam durante o lançamento e a órbita, incluindo vibrações, choques e situações térmicas, tais como temperaturas extremas e condições de vácuo. Todas as três amostras atenderam ou excederam os requisitos, sendo o melhor desempenho de um filtro revestido em prata por meio de um processo eletrolítico.
Além da impressão 3D, a 3D Systems entregou valor agregado que é essencial a esse tipo de projeto, incluindo manuseio de pó certificado, controle de processo para densidade superior do material, pós-processamento comprovado e controle de qualidade confiável.
Booth reconhece que esse conhecimento adicional desempenhou um papel fundamental no sucesso do projeto: "Percebemos que não se trata apenas de utilizar uma boa máquina para fabricar a peça, mas também o resultado de um bom entendimento por parte da 3D Systems do processo de fabricação".
Grande potencial de ROI
Agora que o processo foi validado e as peças atenderam aos mais altos padrões de voo espacial da Airbus Defence and Space, a empresa pode começar a considerar o potencial de retorno do investimento da impressão de metal 3D. O projeto proporcionou o tipo de ROI que encanta um CFO: tempo de retorno mais rápido, custos de produção reduzidos e uma impressionante redução de peso de 50%.
"A massa foi reduzida sem gastar tempo com otimização", afirma Booth, "e pode ser reduzida ainda mais com um design mecânico mais agressivo. A massa reduzida produz economia de custos ao exigir menos propelente no foguete e reduz a demanda nas estruturas de apoio, permitindo maior redução de massa.
"O sucesso deste projeto abre a possibilidade de uma integração muito maior de filtros de RF com componentes mecânicos e térmicos a fim de reduzir o número de peças e a massa geral. Também procuraremos integrar mais funcionalidades, como acopladores de teste como parte do filtro ou diretamente integrados em pistas de guia de onda. Existe um enorme potencial de redução da massa enquanto reduzimos o tempo e os custos de produção".